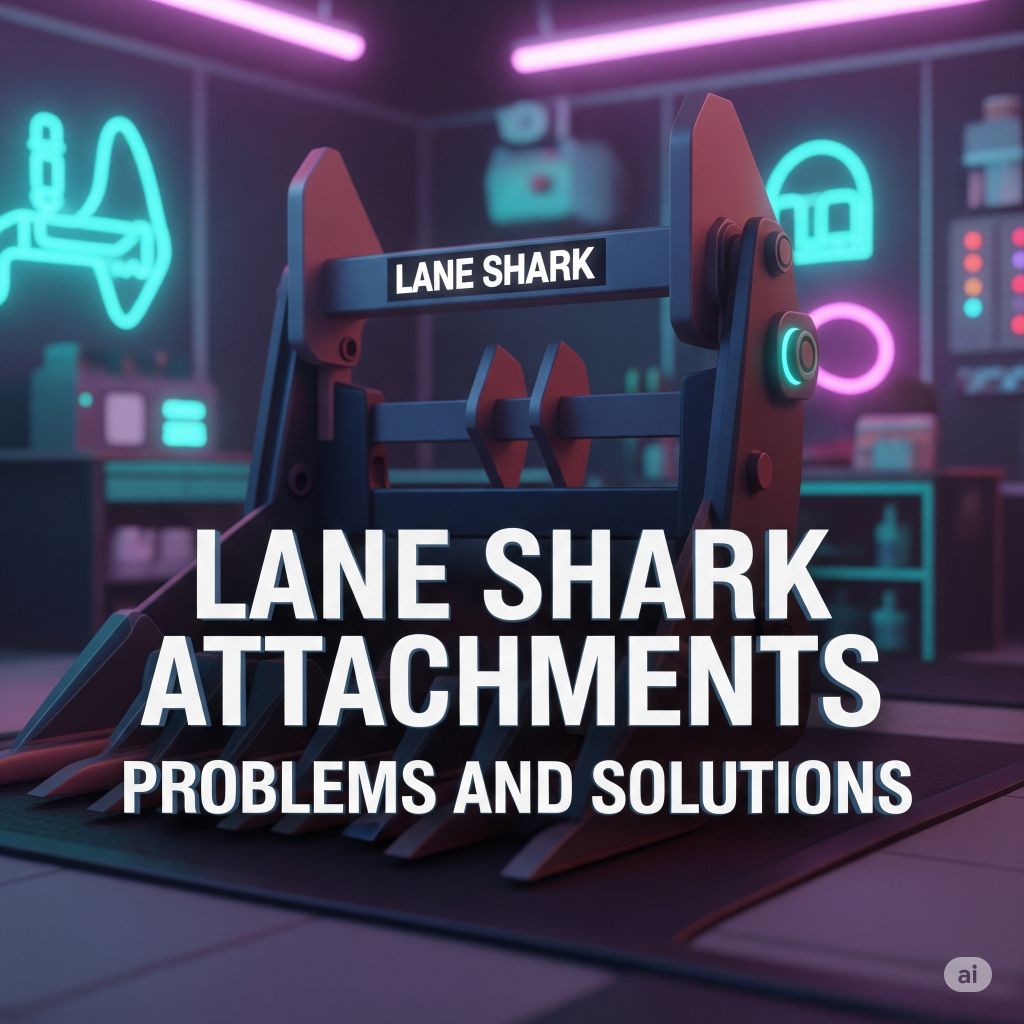
Maintaining Lane Shark attachments for tractors or UTVs can be challenging without a clear troubleshooting roadmap. Designed primarily for light- to moderate-duty trail grooming, roadside trimming, and mulching, these versatile tools excel when used within their intended capacity—but users often push them into heavier workloads.
Improper use, neglected upkeep, and compatibility oversights frequently lead to common failures like blade dulling, guard tearing, fitment issues, and motor strain.
This article provides a deep dive into prevailing issues, detailed diagnostics, step-by-step repairs, and proactive maintenance strategies. By the end, you’ll have all the knowledge needed to extend the life of your Lane Shark attachment and maximize on-field performance.
1. Understanding Lane Shark Attachments
Lane Shark attachments mount to small tractors or UTVs via three-point hitches or dedicated frames, driven by the machine’s PTO. They use rotating blades and protective guards to shred vegetation, groom trails, and clear roadside brush. Although marketed as “light-duty mulchers,” users often treat them like heavy chippers—leading to performance drops and premature wear.
Key design aspects:
- Blades & Hubs: High-speed rotating knives that cut vegetation.
- Blade Guards: Rubber or polymer flaps shielding the cutting chamber.
- Drive Motor/Driveline: Transfers power from the tractor’s PTO shaft to the blade assembly.
- Mounting Interface: Ensures proper alignment and support on the host machine.
2. Common Problems & Underlying Causes
2.1 Blade Dulling and Chipping
Symptom: Vegetation is torn rather than cleanly cut, requiring extra passes.
Causes:
- Contact with rocks, stumps, or metal debris
- Prolonged operation without sharpening
- Inferior aftermarket blade materials
2.2 Blade Guard Tearing and Wear
Symptom: Guards hang loosely or shred entirely, exposing blades.
Causes:
- Overloading in dense brush beyond design capacity
- Abrasion from gravel roads or rocky terrain
- UV degradation of the polymer material over time
2.3 Improper Attachment Fitment
Symptom: Attachment wobbles, misaligns, or shifts during operation.
Causes:
- Incorrect hitch pin size or worn bushing
- Loose mounting bolts or misaligned lifting arms
- Aftermarket adapters not conforming to OEM specifications
2.4 Motor Strain and Overheating
Symptom: PTO stalls, motor bogs down, or warning lights engage.
Causes:
- Operating at too low an engine RPM under heavy load
- Hydraulic flow restrictions in UTV setups
- Insufficient cooling airflow around driveline components
2.5 Parts Sourcing & Replacement Delays
Symptom: Long downtime waiting for OEM parts or substitutes.
Causes:
- Limited dealer networks in remote areas
- Discontinued components after model year changes
- Low inventory of optional heavy-duty blades or guards
3. Step-by-Step Troubleshooting & Repairs
Below is a systematic approach to diagnosing and resolving most common Lane Shark issues.
3.1 Inspect & Sharpen Blades
- Safety First: Park on level ground, turn off engine, remove PTO drive, and allow all components to stop.
- Blade Removal: Loosen hub nuts and slide blades off the spindle. Note orientation for reinstallation.
- Damage Assessment: Look for nicks, bends, or excessive thinning. Minor nicks can be filed; major cracks require blade replacement.
- Sharpening Procedure:
- Secure blade in a vice.
- Use a mill bastard file or angle grinder at manufacturer-specified angle (typically 25–30°).
- Sharpen until you restore a crisp edge, rotating the blade to maintain consistent bevel.
- Reinstallation & Torque: Place blades back, ensuring correct orientation. Torque hub nuts to the spec in your owner’s manual.
3.2 Repair or Replace Blade Guards
- Guard Removal: Unbolt or unclip damaged guards. Inspect anchor points for elongation or cracks.
- Material Upgrade: If you operate on rocky ground, consider heavy-duty rubber or reinforced polymer guards rated for abrasion.
- Installation Tips:
- Use anti-seize compound on mounting bolts.
- Tighten evenly to avoid twisting the guard.
- Ensure a ½-inch clearance between guard tips and housing.
3.3 Correct Attachment Fitment
- Bushing & Pin Check: Remove hitch pins; measure bushing inner diameter vs. pin thickness. Replace worn bushings (>0.020″ clearance) or use oversize Grade-8 pins.
- Bolt Inspection: Retorque all mounting and lifting arm bolts to spec; replace any with visible thread damage.
- Alignment Verification:
- Raise and lower the implement slowly, watching for tilt or binding.
- Adjust lift arm length or top link until the cutter housing is level in the side-to-side and fore-aft planes.
3.4 Alleviate Motor Strain
- PTO Speed Check: Confirm tractor RPM under load meets the attachment’s rated PTO speed (commonly 540 RPM).
- Hydraulic Flow (UTV Only): Measure hydraulic pressure and flow to motor; verify against attachment requirements (e.g., 3 GPM at 2,000 PSI). Clean or replace filters if flow is low.
- Cooling Measures:
- Install deflector plates or additional airflow ducts to channel cooling air around the driveline housing.
- Check bearings for heat discoloration—replace any that show blueing or scoring.
4. Proactive Maintenance Schedule
Creating a routine maintenance regimen prevents many problems before they occur. Below is a suggested schedule for moderate-use operators:
Interval | Task |
---|---|
Daily | Clean debris from housing; inspect for visible damage |
Every 10 Hours | Check blade torque; inspect guards & replace fasteners |
Every 25 Hours | Lubricate driveline grease fittings; inspect PTO shaft |
Every 50 Hours or Monthly | Remove blades; sharpen or replace as needed |
Every 100 Hours or Quarterly | Inspect internal gearboxes; change lubricant if applicable |
Annually | Replace seals, bearings; pressure-wash housing thoroughly |
Tip: Keep a maintenance log book in your tractor’s glovebox. Record dates, hours, and parts replaced to track wear patterns.
5. Upgrades and Aftermarket Options
While OEM parts ensure compatibility, savvy owners sometimes invest in beefed-up components:
- Premium Blades:
- High-Carbon Steel: Better edge retention in brush work.
- Carbide-Tip Blades: Ideal for rocky or stony terrain; however, they’re costlier and can stress hubs if used improperly.
- Reinforced Guards:
- UV-Stabilized Rubber: Resists cracking in sun-exposed applications.
- Polyurethane Flaps: Longer life in abrasive conditions.
- Heavy-Duty Drivelines: Some third-party vendors offer reinforced shafts and couplers rated for higher torque, reducing flex and vibration.
- Quick-Change Mounting Kits: Allows swapping between flail, brush, and mower attachments within minutes—minimizing downtime.
6. Compatibility Checklist
Before purchasing or mounting a Lane Shark attachment, verify:
- Tractor/UTV Horsepower: Must meet or exceed the minimum rating (commonly 25–40 HP).
- PTO Type & Speed: 540 vs. 1,000 RPM—ensure correct spline count and coupling.
- Three-Point Hitch Category: Category 1 vs. Category 2—match ball sizes and lift capacity.
- Hydraulic Supply (if applicable): Confirm flow and pressure match motor requirements.
- Frame Clearance: Guarantee no interference between attachment housing and tractor chassis or roll-over bar.
7. Parts Sourcing Strategies
Delays in obtaining replacement parts can cripple operations. Consider these sourcing tactics:
- Authorized Dealers: Place standing orders for consumables (blades, belts, guards) before the season starts.
- Cross-Reference OEM Numbers: Use blade or bearing numbers to find compatible parts in agricultural or industrial suppliers.
- Aftermarket Suppliers: Some specialize in high-wear components with faster shipping. Always check fit tolerances before purchase.
- Community Networks: Join tractor-owner forums or local equipment co-ops for “loaner” parts or bulk-buy deals.
8. Advanced Diagnostics & When to Seek Professional Help
8.1 In-Field Vibration Analysis
Excessive vibration can indicate bent spindles, misaligned driveline, or worn bearings. Use a simple vibration meter or smartphone app:
- Record baseline vibration at idle and full load.
- A sudden increase (>20 %) suggests mechanical degradation.
8.2 Motor Current Monitoring (UTV Hydraulic Models)
Install ammeters on the hydraulic circuit to track motor draw. A steady rise in current draw signals internal wear or blockage.
8.3 Professional Rebuilds
If:
- Gearbox Leaks Persist after seal replacement
- Spindle Bearing Clearance exceeds tolerances even after bearing swap
- Cracks in Housing due to impact or fatigue
…then consult a reputable agricultural machinery repair shop. They can perform press-fit bearing installs, weld housing cracks, and rebalance rotors to OEM specifications.
9. Safety Best Practices
- Always shut off the engine, disengage PTO, and lock out power before service.
- Wear cut-resistant gloves when handling blades and guards.
- Avoid “live” sharpenings—secure blades in a vice and disconnect all power sources.
- Keep bystanders at least twice the cutting radius away when operating.
- Follow the manufacturer’s torque specs to prevent loose parts from becoming projectiles.
10. Real-World Case Studies
Case Study A: Trail Crew in Oregon
- Problem: Guards shredded within five hours of rocky trail mowing.
- Solution: Switched to UV-stabilized neoprene guards and reduced tractor speed by 15 %. Guard life increased to 50 hours.
Case Study B: Vineyard Understory Management
- Problem: Blades dulled quickly on vine pruning debris.
- Solution: Adopted carbide-tip blades, rotated sets every 25 hours, and instituted daily debris cleaning. Productivity rose by 30 %.
11. Conclusion & Key Takeaways
Proper use and disciplined maintenance are the cornerstones of Lane Shark longevity. To recap:
- Inspect Daily for damage and debris build-up.
- Sharpen Blades frequently and replace guards before they fail completely.
- Ensure Fitment matches tractor specs to prevent misalignment.
- Monitor Load via PTO speed, hydraulic draw, and vibration metrics.
- Source Parts Proactively to avoid downtime.
- Use Safety Gear and lock out power when performing service.
By adhering to these guidelines—coupled with targeted upgrades where needed—you’ll keep your Lane Shark attachment performing at peak efficiency for years to come.
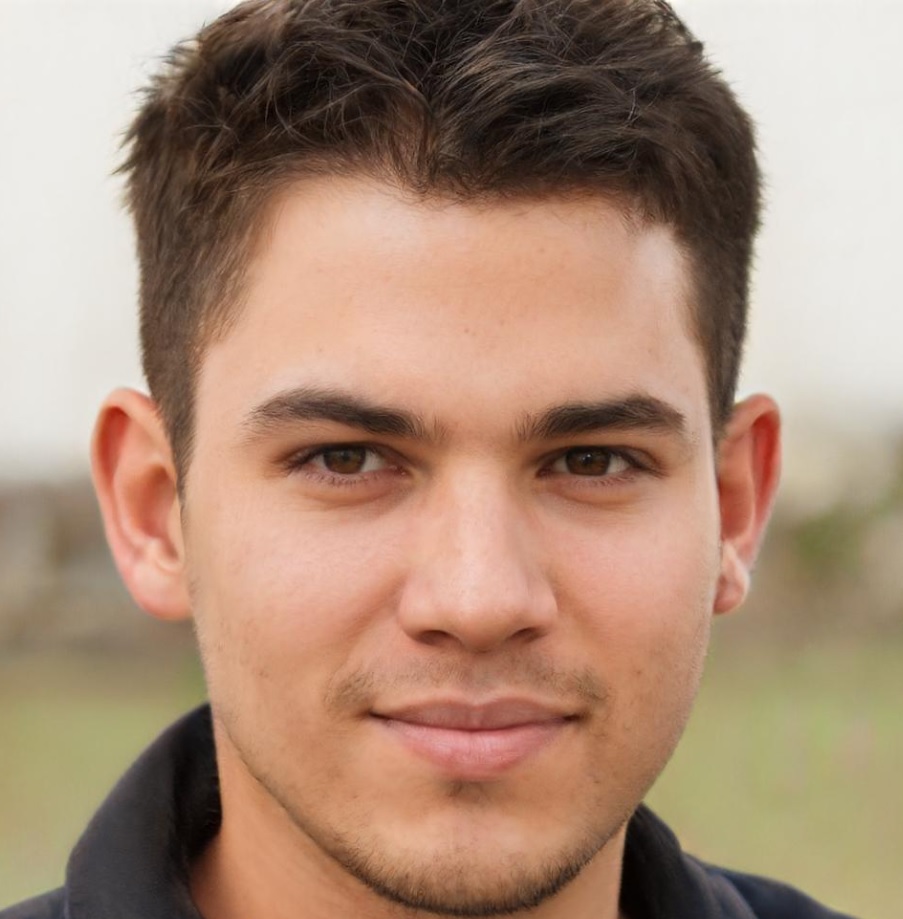
I’m David man behind Lawn Mowerly; I’ve been dealing with lawnmowers and Tractors with my father since I was a kid. I know every make and model and what each one is capable of and love helping people find the perfect equipment for their needs.