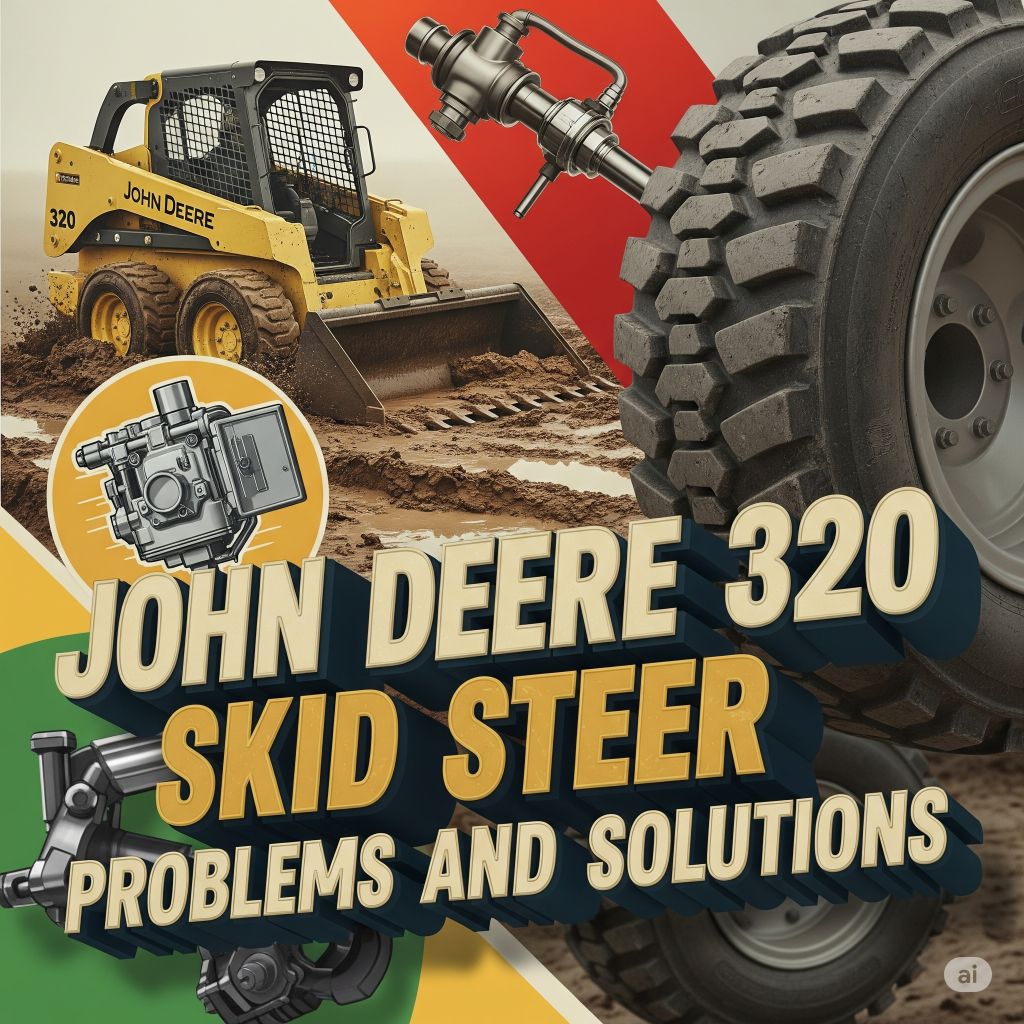
The John Deere 320 skid steer loader—renowned for its durability, compact size and versatile attachments—is a work on job sites, farms and landscaping projects. Powered by a 72 HP Yanmar diesel engine and a hydrostatic drive, it handles grading, digging, trenching and material handling with ease. However, like any rugged equipment, the 320 can develop issues if pushed beyond limits or neglected in maintenance. This article delivers an in-depth, step-by-step manual covering:
- Core design & specifications
- Common failures and their root causes
- Detailed troubleshooting & repair procedures
- Proactive maintenance schedule
- Recommended upgrades & aftermarket options
- Parts-sourcing strategies
- Safety best practices
- Real-world case studies
- Key takeaways
By applying these insights, you’ll maximize uptime, extend component life and keep your 320 performing at peak efficiency.
1. Overview & Key Specifications
The 320 skid steer features:
- Engine: Yanmar 4TNV88-HT, 72 HP at 2,500 RPM, liquid-cooled, four-cylinder diesel
- Hydraulic System: Dual-pump load-sensing system, 21 GPM each pump, 3,000 psi maximum
- Drive: Hydrostatic, planetary final drives, high-flow option (up to 49 GPM total)
- Operating Weight: ~6,550 lb (with bucket)
- Lift Capacity: Rated Operating Capacity (ROC) 2,000 lb; tipping load 4,000 lb
- Auxiliary Hydraulics: Standard flow 21 GPM; high-flow 38 GPM
- Dimensions: Width 66 in, Height 75 in, Length w/bucket 122 in
Application: Excavation, grading, material handling, brush cutting (with mulcher), snow removal.
2. Common Problems & Root Causes
- Hydraulic Leaks & Loss of Power
- Worn rod seals in lift cylinders
- Loose or damaged hose fittings
- Contaminated hydraulic fluid damaging valves
- Erratic Joystick Controls or Stiction
- Air in hydraulic lines
- Worn spool valves in control manifold
- Dirty or degraded hydraulic fluid
- Engine Overheating & Coolant Loss
- Clogged radiator fins or oil cooler cores
- Failed thermostat or water-pump bearing
- Radiator cap seal leakage
- Drive System Slippage or Squeal
- Worn drive belt on cooling fan
- Hydrostatic pump charge-pump failure
- Air ingress in hydro drive lines
- Electrical Faults & Stall-Outs
- Corroded battery terminals or poor ground straps
- Faulty alternator/regulator not charging battery
- Damaged wiring harness in swing-open panels
- Attachment Coupler Misalignment
- Loose mounting bolts or worn bushing in quick-attach
- Bent coupler frame from side loading
- Excessive Vibration & Noise
- Unbalanced cooling fan or engine pulley
- Damaged engine mount bushings
- Foreign debris in radiator or drive fan
3. Troubleshooting & Repair Procedures
3.1 Hydraulic Leak Repair
- Visual Inspection
- Park on level ground, lower implements, shut off engine and relieve system pressure.
- Wipe cylinder rods and hoses; cycle boom several times and watch for fresh seepage.
- Seal/Cylinder Service
- If rod seal leaks, remove cylinder, disassemble per JD service manual, replace seals and wipers.
- Reassemble with clean lube, torque caps and test at low pressure before full-load use.
- Hose & Fitting Replacement
- Replace hoses older than 2 years or showing abrasion.
- Use OEM high-pressure hoses; torque fittings to 18 ft-lb.
3.2 Joystick & Spool-Valve Remedies
- Bleed Air from Circuit
- Open bleed port on control manifold; operate joysticks slowly until fluid runs without bubbles.
- Fluid & Filter Change
- Drain hydraulic tank; replace inline and return filters.
- Refill with JD Hy-GARD fluid; run engine to operating temp and top off.
- Spool Valve Rebuild
- Remove manifold per service manual; inspect spools for scoring.
- Install new O-rings/seals; re-lap spools if minor scoring, or replace if severe.
3.3 Engine Cooling System Service
- Radiator & Oil Cooler Cleaning
- Remove front grille; use low-pressure wash to clear fins front and back.
- Straighten bent fins with fin comb; replace core if corrosion is severe.
- Thermostat & Pump Inspection
- Swap thermostat with known-good unit; spin water-pump pulley to check bearing play.
- Replace pump if rough or leaking.
- Coolant System Pressure Test
- Pressure-test radiator cap and fill port to 15 psi; replace cap if it fails to hold pressure.
3.4 Drive System Maintenance
- Fan Belt Inspection
- Check tension (½″ deflection at midpoint) and wear; replace crisp-cracking belts.
- Charge Pump Check
- Monitor pressure at test port—should be ≥100 psi when cold.
- Replace charge-pump if pressure is below spec or fluctuates.
- Hydro-Line Air Purge
- Run engine at idle; loosen test ports to bleed air in charge lines until smooth.
3.5 Electrical Diagnostics
- Battery & Ground Audit
- Clean and tighten battery terminals; replace cables with <50 mΩ internal resistance.
- Install 4 AWG ground strap between engine block and chassis.
- Alternator/Regulator Test
- Measure charging voltage (13.8–14.5 V with engine at 2,000 RPM).
- Replace regulator if voltage is out of range.
- Harness & Fuse Inspection
- Open side panels; route harness away from high-heat and pinch points.
- Replace brittle wires and corroded connectors; verify fuse block tightness.
3.6 Coupler & Attachment Alignment
- Bolt & Bushing Check
- Tighten coupler-to-frame bolts to 60 ft-lb; inspect bushing wear (>0.030″ clearance = replace).
- Frame Straightness
- On a flat surface, measure coupler plate alignment; if bent, send coupler to weld-shop for re-plating.
3.7 Vibration & Noise Mitigation
- Fan & Pulley Balancing
- Mark pulley weights; use stick-on balancing weights to eliminate wobble.
- Mount Bushing Replacement
- Jack under loader arm; remove and replace engine and transmission mount bushings.
- Debris Removal
- Check under-hood and behind radiator for sticks/rocks; keep intake areas clear.
4. Proactive Maintenance Schedule
Interval | Task |
---|---|
Daily (Pre-Start) | Check engine oil, coolant, hydraulic fluid; inspect hoses/belts |
Every 50 Hours | Grease all zerks; torque lug studs; inspect tires or tracks |
Every 100 Hours | Change engine oil & filter; clean/replace air filter element |
Every 200 Hours | Replace hydraulic filters; flush reservoir if fluid dark/cloudy |
Every 500 Hours | Replace coolant; service water pump; test radiator pressure |
Annually | Inspect hydro pumps & motors; replace hydro charge pump |
Pro Tip: Maintain a simple log—record hours, dates and any corrective actions to identify recurring issues early.
5. Upgrades & Aftermarket Enhancements
- High-Flow Hydraulic Kit: Boost auxiliary output from 21 GPM to 38 GPM for high-demand attachments
- Heavy-Duty Radiator Core: Aluminum aftermarket cores resist corrosion and improve cooling
- Sealed Joystick Assemblies: Prevent dirt intrusion and stickiness in dusty environments
- LED Work Lights: Reduce electrical load and enhance night-time visibility
- Vibration-Damping Mounts: Polyurethane bushings under cab and engine minimize noise and extend mount life
6. Parts-Sourcing Strategies
- John Deere Dealer: Genuine filters, seals, hoses and electronic modules
- Industrial Suppliers: Cross-reference JD part numbers with SKF bearings, Gates belts and Parker hoses
- Online Marketplaces: Sites like Parts.Cat.com or UBuildItShop.com stock aftermarket hydraulic components at competitive prices
- Local Machine Shops: Rebuild cylinders, fabricate custom brackets or rebalance pulleys expedite downtime in remote locations
Always confirm your machine’s serial number (inside cab on left-hand panel) before ordering parts.
7. Safety Best Practices
- Lockout/Tagout: Remove key, lower boom and relieve all systems before working.
- Hydraulic Safety: Wear gloves and eye protection when bleeding lines—high-pressure fluid can penetrate skin.
- Lifting & Jacking: Support frame with rated stands; never rely on hydraulic locks alone.
- PPE: Use cut-resistant gloves around belts, and hearing protection during noisy operations.
- Fire Prevention: Keep radiator fins clear of dry vegetation; inspect fuel lines for chafing.
8. Real-World Case Studies
Case Study A: Rapid Hydraulic Leak
- Symptom: Sudden drop in lift performance, visible oil spray at hose crimp.
- Diagnosis: Crimp nut had backed off due to vibration, tearing hydraulic sleeve.
- Solution: Replaced hose assembly with Parker Storm™ series, installed thread-lock anti-vibration compound, retorqued to spec. Leak-free after 1,200 hours.
Case Study B: Joystick Stiction in Cold Climate
- Symptom: Controls froze in place at low temperatures, causing erratic lift movement.
- Diagnosis: Water condensation in control manifold freeze-thawed, degrading seals.
- Solution: Installed manifold heater kit, switched to low-moisture hydraulic fluid, added breather dryer. Controls remained smooth through winter.
9. Conclusion & Key Takeaways
- Detect Early: Address leaks, overheating and controls issue at first sign to avoid costly cascade failures.
- Maintain Rigorously: Adhere to the defined intervals for fluids, filters, greasing and inspections.
- Upgrade Smartly: High-flow kits, sealed controls and heavy-duty cores tailor the 320 for demanding tasks.
- Source Wisely: Blend genuine Deere parts with quality industrial components to optimize cost and availability.
- Safety First: Always de-energize, relieve pressure and use proper supports and PPE.
By following these structured troubleshooting steps, maintenance schedules and targeted enhancements, your John Deere 320 skid steer will deliver reliable performance year after year—maximizing productivity and protecting your investment.
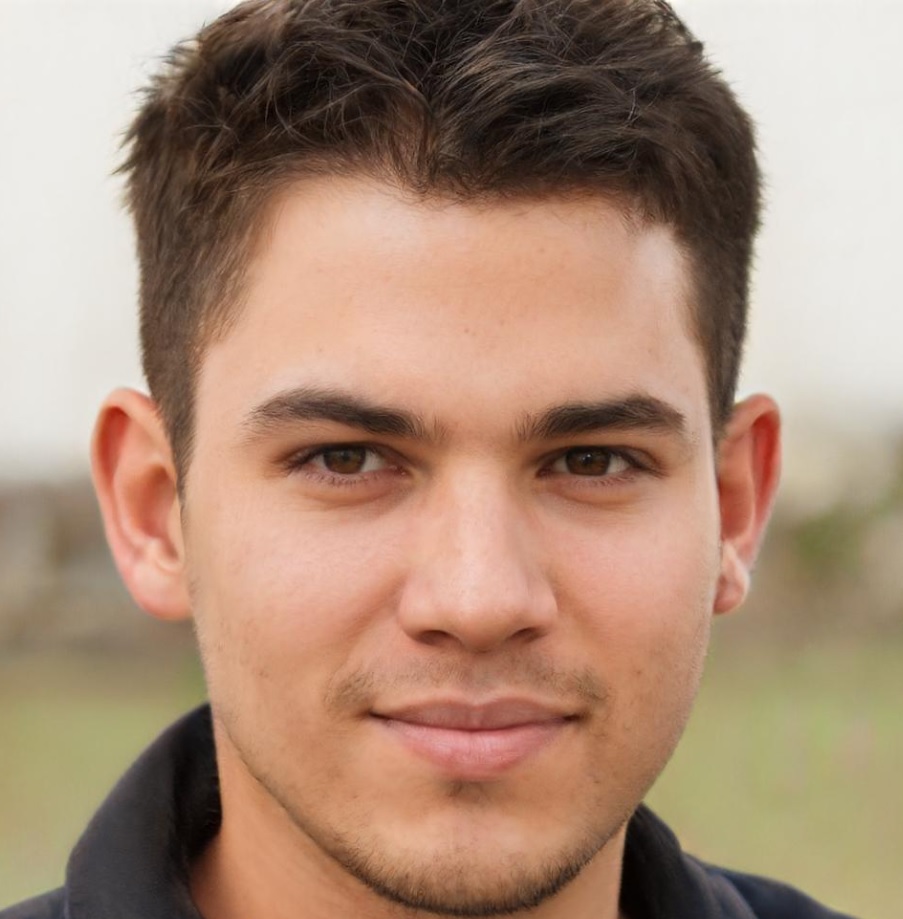
I’m David man behind Lawn Mowerly; I’ve been dealing with lawnmowers and Tractors with my father since I was a kid. I know every make and model and what each one is capable of and love helping people find the perfect equipment for their needs.